In June 2024, YINUOLINK's three-year product planning was formally completed, laying a solid foundation for future overall development.
Strategic transformation,planning for the future
As technology changes with each passing day and the international market environment becomes increasingly severe, the sustainable development of enterprises is inseparable from a clear strategic direction to cope with constant market changes and challenges. As a communication equipment supplier with rich hardware customization experience and pioneering and innovative spirit, YINUOLINK has a keen insight into future product planning and market positioning, aiming to meet market demand and enhance product competitiveness. In 2021, we decided to officially transform into consumer finished products market and formulate product planning goals for the next three years.
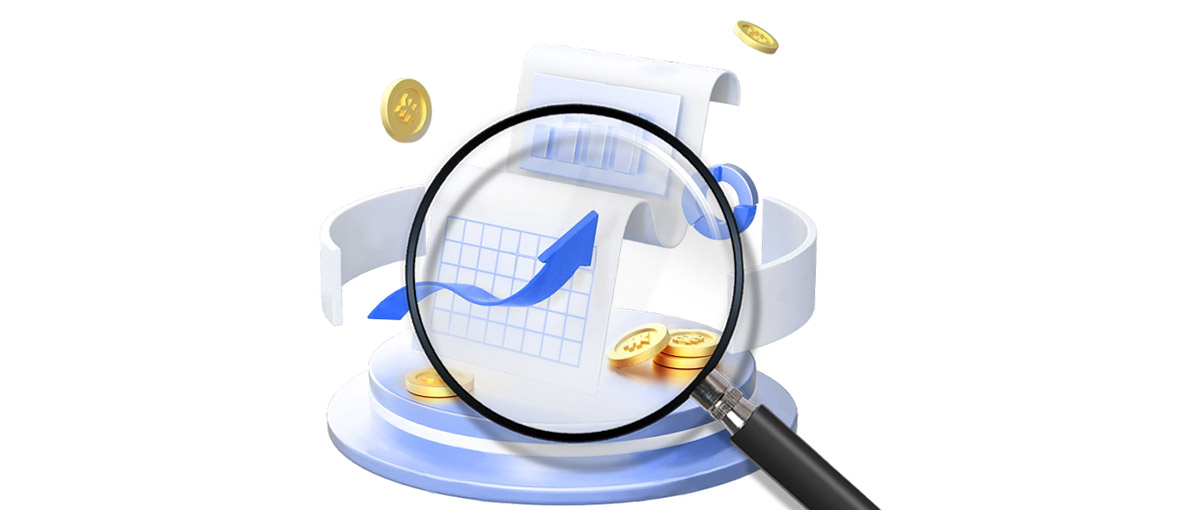
The road to transformation is rife with challenges
In this transformation, YINUOLINK will undoubtedly face many challenges. First of all, Fierce competition in the consumer finished goods market, and consumers are increasingly demanding product quality, performance and experience. Secondly, the COVID-19 faced during this period has invisibly put huge pressure on the production and supply chain of enterprises. This is coupled with the fact that YINUOLINK had previously focused primarily on hardware customization and had little real-world experience in the consumer finished goods market space.Not only does the company need to have strong R&D capabilities, but it also needs to have keen insight into market demand, efficient supply chain integration capabilities, flexible decision-making capabilities, and close teamwork.
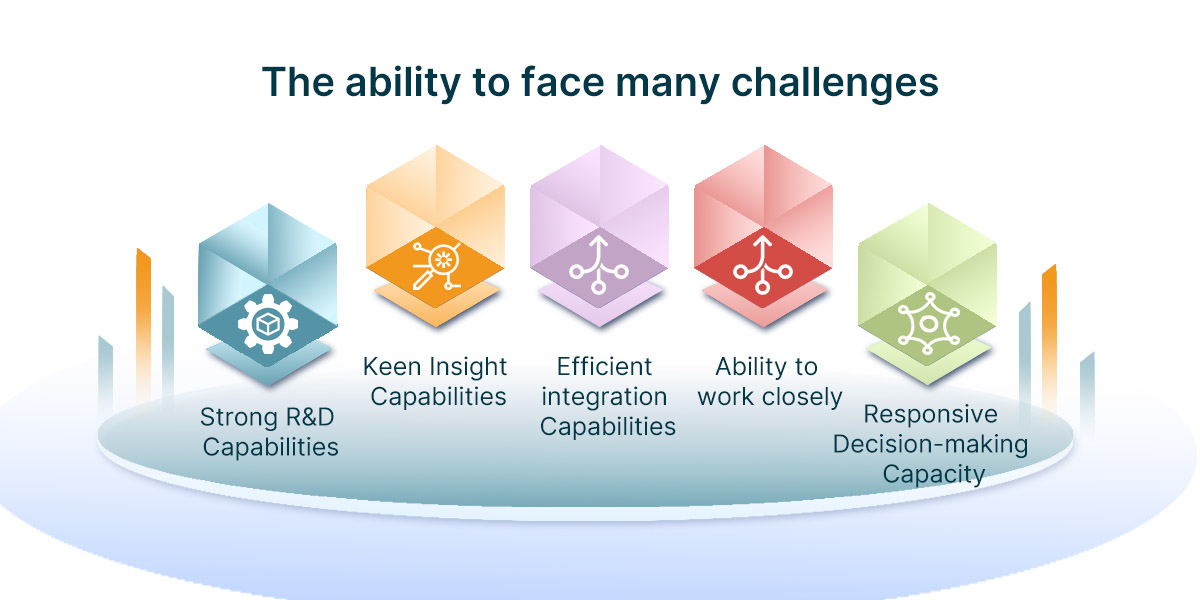
Forge ahead and implement precise policies
Setting goals and going all out
Faced with such challenges, YINUOLINK vigorously researched the market and analyzed customer needs in the early stage, and formulated development strategic target routes for wireless routers, 4G/5G wireless routers, wifi extenders, network cards and other series of products to meet the diversification of different user’s demand. During the research and development period, R&D funds were invested multiple times and accumulated up to tens of millions. Even during the COVID-19 and the severe economic environment last year, YINUOLINK remained down-to-earth, always followed its own pace, went all out to make breakthroughs in R&D, and never stopped. During this period, the product has undergone multiple mold modifications, structural confirmation, heat dissipation effect and antenna matching, hardware, software, etc., which have been repeatedly modified and verified in order to create the most outstanding product.
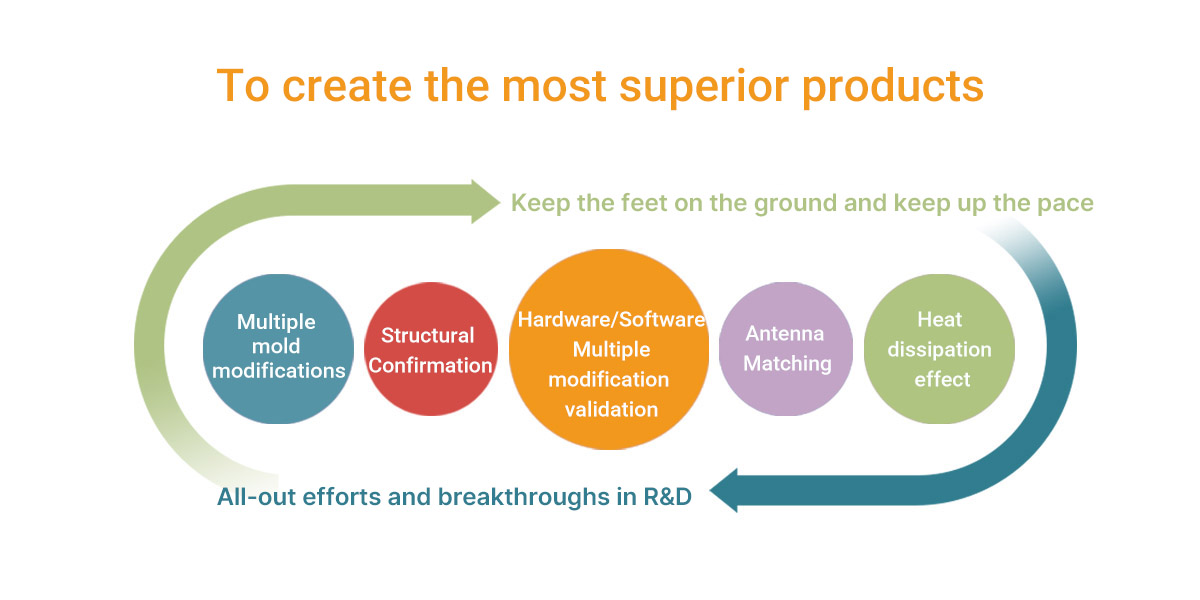
A new journey of refined management
While in-depth research and development of the complete machine, we realized the importance of organizational structure processes, and began to comprehensively promote the company's gradual move from extensive management to refined management in early 2023. YINUOLINK not only initiated the reform of the meeting model, but also promoted the meeting model of "discussing and solving the problems raised in an open and free way", which greatly shortened the meeting time and solved the problem more effectively. It also emphasizes that "meetings must be discussed, discussions must be acted upon, actions must be decided, and decisions must be results", so that meetings are no longer just a formality, but truly become an effective means to promote work progress. At the same time, we put forward the work concept of "paying attention to details", treat every task with a rigorous attitude, and strive for excellence to avoid repeated things. The "Ten Minute Response Method" has also been implemented to achieve rapid response and active handling among teams, creating a good working atmosphere in which "everything is explained, everything is settled, and everything is responded to", which is not only conducive to increasing team cohesion, but also Can improve work efficiency and ensure work quality. The communication mode of corporate mailbox and corporate WeChat is enabled, which effectively promotes efficient communication and collaboration of the team, creating great convenience for the continuity of work and retrospective inquiry. In addition, the company's overall administrative rules and regulations, as well as the process system of each department to carry out a full range of detailed combing work.
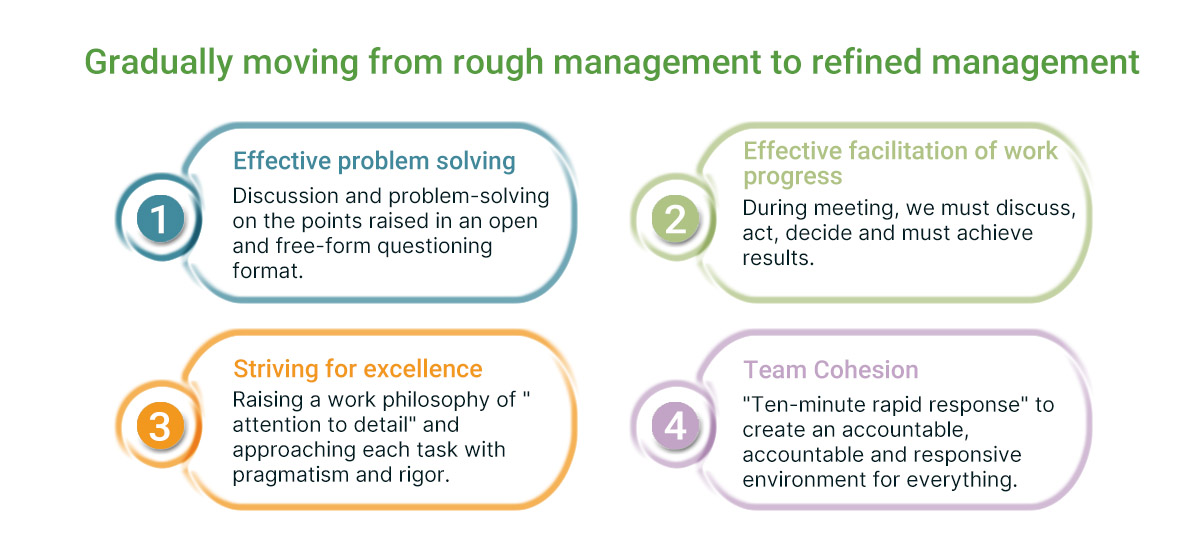
Remarkable achievements and impacts of R&D reform
For the entire R&D process from project establishment to completion, a rigorous and detailed "R&D Process and Management System" has been formulated, which clearly clarifies the job responsibilities and work processes of R&D personnel. During this reform process, the R&D department focused on supplementing a large amount of previously missing important information, such as the "Project Establishment Information", which can clearly state the background, objectives, expected results and required resources and other key information of the project, providing a strong support for the accurate positioning and smooth launch of the project, making the project establishment more scientific and reasonable. "Product Certification Information" confirms that products comply with various strict standards and regulations and improves the market access rate of products. The "RF Test Report" provides reliable data support for the product's wireless communication function, effectively reducing radio frequency-related faults and problems. The "Product Specification for Approval" provides a clear basis for product delivery and acceptance, greatly shortening the delivery and acceptance time. "Software Test Cases" cover various functions and performance indicators of the software, ensuring the stability and reliability of the software, and significantly reducing the failure rate of the software. This not only significantly improves the standardization and rigor of R&D work, making the R&D process more clear and controllable, but also shortens the cycle of new product development, reasonably controls the R&D costs, and lays a solid foundation for the efficient operation of the entire R&D department and the smooth progress of the project.

In the research and development stage, comprehensive and in-depth product performance tests are conducted, such as "Wireless Distance Speed Test Comparison of Products with The Same Chipset", "Outdoor Distance Flow Speed Test", "Throughput Test - Shielded Box and Open Environment", "Product Drop Test", "One-minute Constant Cycle Oower-off and Restart Shock Test of 10,000 Times", "A Week of Real Internet Operation and Broadband Speed Test", "Various Software Mode Tests", "Wireless and Wired Speed Test of The 4G/5G Operators", Accurately grasping the actual performance of the product in various environments helps the R&D team to optimize and improve the product in a targeted manner to enhance the performance and stability of the product, and also provides valuable experience and reference for the development of subsequent products.
BOM changes are frequent as the product is continuously improved and optimized. The R&D team is always on the alert to rigorously and meticulously implement the standard specifications of the "BOM, ECN Change Workflow Management System" to ensure that the relevant technical documents are synchronized and updated with the BOM changes to avoid production errors. At the same time, it helps us accurately control material purchasing and inventory levels, avoiding the phenomenon of stagnant materials and stock-outs caused by changes, and reducing inventory costs. It also provides detailed historical records for the subsequent investigation of quality problems, cost accounting, process improvement, etc., tracing the root causes of problems, summarizing lessons learned, and continuously improving the management system.
To ensure the complete archiving of R&D data, the standard specification "R&D Project Document Management Specifications" has been specially established, clarifying the data management structure and classification standards.
In the actual work process, the R&D team can meticulously and strictly implement this specification, which not only strongly protects the R&D data ensuring their completeness, accuracy and standardization, but also makes the R&D work process more standardized and orderly, effectively reduces the risk of data confusion and loss, and forms a good protection for core technologies and commercial secrets, so that they are avoided from being leaked.
It helps to accumulate R&D experience, provides valuable reference and strong data support for new R&D projects, prevents potential problems and risks in advance, reduces the possibility of duplication of labor, greatly improves R&D efficiency, shortens the R&D cycle, and provides a solid guarantee for the company's stable development and long-term interests.
It helps to effectively track and monitor R&D projects, and can promptly discover problems and deficiencies in the R&D process, thereby promoting the continuous optimization and improvement of R&D work.
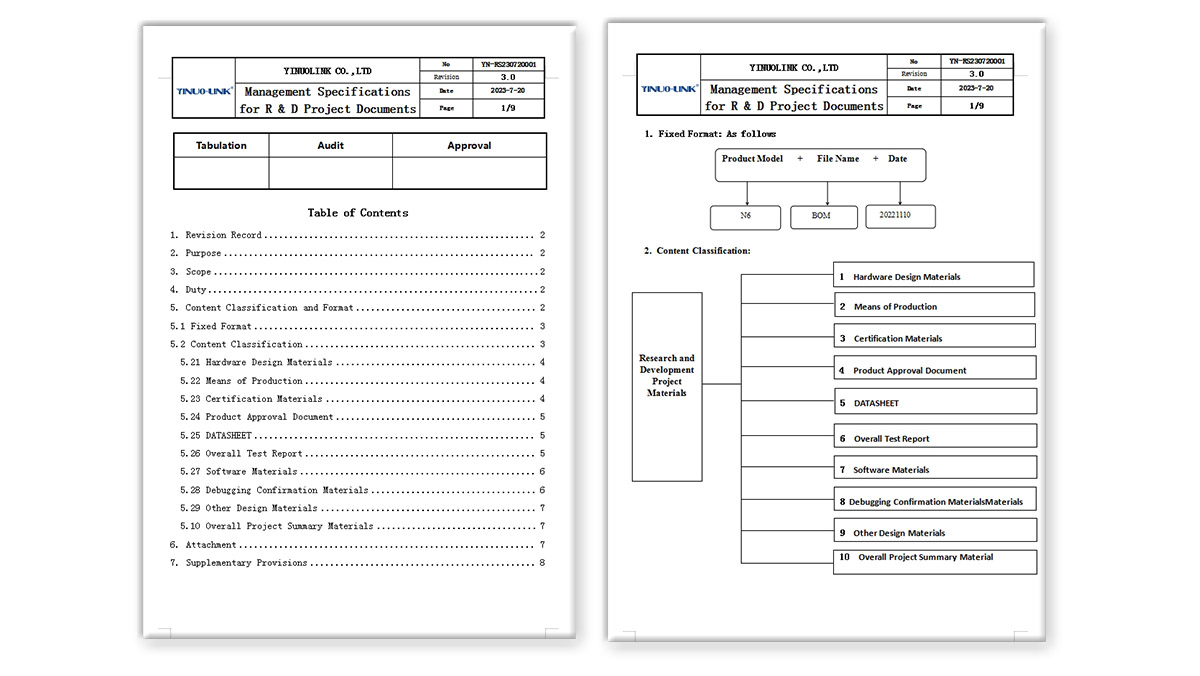
Behind these R&D reforms, it not only pours a lot of efforts and endeavors of R&D personnel, but also reflects the persistent pursuit of technology and unremitting exploration of innovation. Faced with various technical difficulties and challenges, we never flinched. Relying on our solid professional knowledge and rich experience accumulated through countless attempts and failures, we went all out to overcome difficulties time and time again and achieved technological breakthroughs one after another. Help YINUOLINK to stand out in the fierce market competition, and constantly launch competitive products and solutions to win customers' trust and market recognition.
Corporate charm, multi-dimensional display
Make up for the lack of human resources management processes and systems, and build a more complete system of rules and regulations and welfare benefits to regulate the internal behavior and processes of the enterprise, to ensure that the operation of the enterprise is standardized and efficient. Make comprehensive and in-depth rational allocation of resources, whether human, material or financial, to achieve precise allocation to achieve the maximum benefit of resources. Standardize the sending, receiving, archiving and management of documents, and formulate rigorous and detailed operating procedures and standards to ensure the accurate transmission and timely storage of information. Strengthen personnel training and talent introduction, formulate a systematic and comprehensive talent training program, and actively introduce external outstanding talents to inject fresh blood and innovative vitality into the enterprise in order to enhance the overall quality and innovation ability of the team and provide strong talent support for the sustainable development of the enterprise.
At the same time, a special patent and product display area is set up, in which all the patent certificates and representative quality products owned by YINUOLINK are centrally displayed. Through such an intuitive and vivid display, not only can visitors understand at a glance the remarkable achievements made by YINUOLINK in technological innovation and product research and development, but also feel it’s persistent pursuit of quality and unremitting efforts for innovation. We have always been user-centered, constantly innovating and making progress, and are committed to providing users with high-quality products and services.
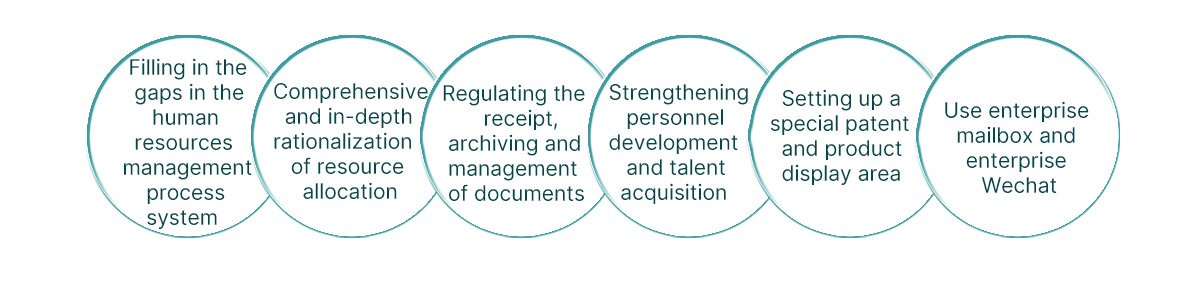
Financial management, comprehensive upgrade
Optimize the financial system, from every penny of income to every bit of expenditure, everything is classified, calculated and analyzed in detail. Every PO, PI, CI etc. is scrutinized to ensure that it is legal, compliant and reasonable. Every expense reimbursement goes through layers of approval, following established processes and systems to eliminate any possible waste and fraud.
Comprehensive cost accounting for each batch of products helps enterprises to accurately price, optimize resource allocation and provide strong support for decision-making, while also effectively controlling costs, improving operational efficiency, reducing risks, enhancing market competitiveness and achieving sustainable development.
Preparation of financial statements: such as the Balance Sheet, Income Statement and Cash Flow Statement, each of which clearly shows the financial position and operating results of the enterprise, with detailed explanatory notes behind each figure explaining its source and composition, so that managers can accurately understand the financial position of the enterprise.
In terms of asset management, asset inventories have been increased to twice a year to identify and fill gaps. For fixed assets, the standard specification of "Fixed Asset Coding Management Rules" has been established to clarify the classification standards and coding system of fixed assets, which is conducive to the financial accounting of assets and depreciation calculation. Establish a "Fixed Asset Ledger" to clarify asset management responsibilities and location and other detailed asset information, which can quickly locate and inventory assets and improve the efficiency and accuracy of inventory work. Whether it is purchasing and accepting, transferring or scrapping, all of them are executed in strict accordance with the process system, so that each link can be followed, thus realizing the fine management of the asset life cycle, ensuring the safety, integrity and effective use of the assets, so that each asset can play a maximum benefit in production and operation, and providing a solid material foundation for the stable operation and sustainable development of the company.
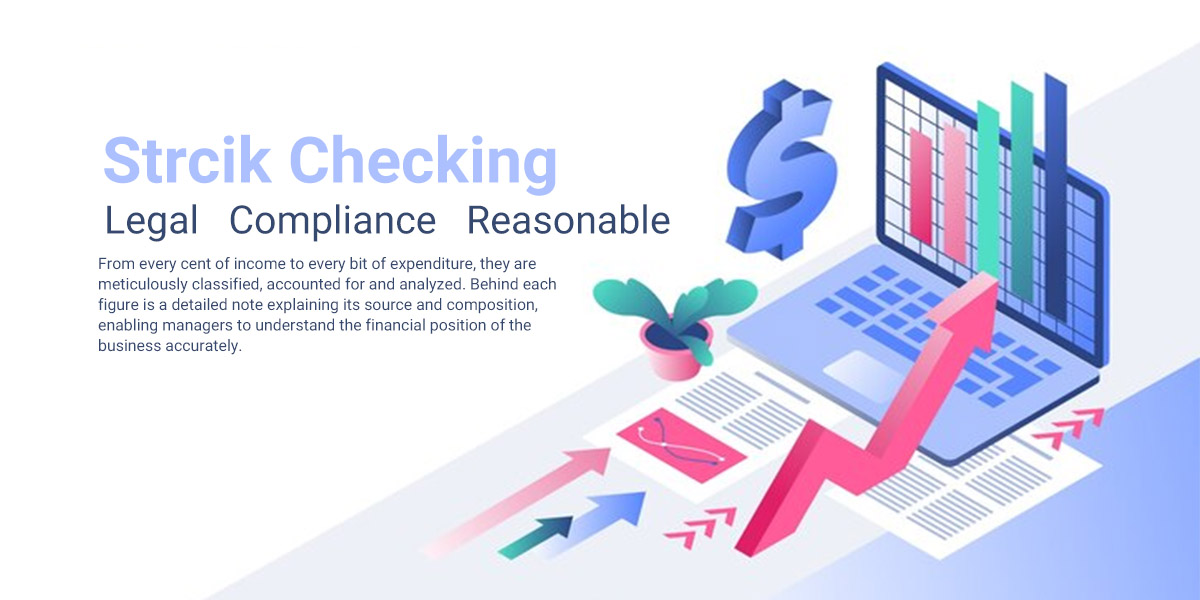
Material control, a new breakthrough
Abandoning the original material coding rules and re-establishing a more comprehensive set of material coding usage rules, the ERP system has become more standardized and transparent after being regulated. In this way, the required material information can be quickly obtained, significantly reducing data confusion and errors. At the same time, key aspects such as inventory status, procurement progress, and production needs can be accurately grasped, greatly enhancing the accuracy and reliability of material management. It also helps to strengthen communication and collaboration within the enterprise, reducing misunderstandings and delays caused by poor information, thereby further improving the overall operational efficiency and management level of the enterprise.
Comprehensively sort out and optimize the "Warehouse Process and Management System" to strengthen the full tracking and monitoring of materials. Whether it is shipping, warehousing, picking, scrapping, borrowing or returning, every link is strictly implemented in accordance with the process system to ensure that the real-time status of raw materials is clear and traceable. This not only avoids the loss of materials, confusion, waste of resources and inventory backlog, but also ensures that the raw materials needed for production can be supplied in a timely manner and in sufficient quantities, so that the entire production process is as smooth as running water. The inventory and liquidation of materials not only accurately grasp the actual status of corporate assets, but also promptly discover loopholes in material management, effectively promoting the standardization and refinement of material management.
Material acceptance is strictly in accordance with the newly developed "Quality Inspection Standard Specification" and "Sampling Standards", and issue the corresponding "Acceptance Inspection Report" to ensure the quality of incoming materials, which not only effectively enhance the production yield, so that the production process is always in a tightly controlled state, to provide a reliable guarantee for the quality of the product, but also significantly reduces the unnecessary production costs. For defective products, timely issue the "Quality Abnormalities Contact Letter", actively communicate with suppliers, prompting suppliers to pay attention to and improve the quality of their products, and continuously improve the material supply chain, so as to further optimize the quality of the supply chain.
Optimize production processes and strictly enforce quality control management
To prepare for the goal of achieving a defective rate of 5 out of 10,000, the R&D team gives full play to its deep expertise, makes precise adjustments to the parameters of the production process and repeatedly verifies them, and carries out repeated start-up tests and wireless calibrations for each product. Taking WiFi calibration as an example, the R&D team conducts in-depth research on debugging power parameters without sparing any details, and comprehensively analyzes the data generated from each test, aiming to continuously improve the limit standards of WiFi so as to ensure that there is enough margin in the subsequent production process to ensure smooth production and high-quality delivery of products.
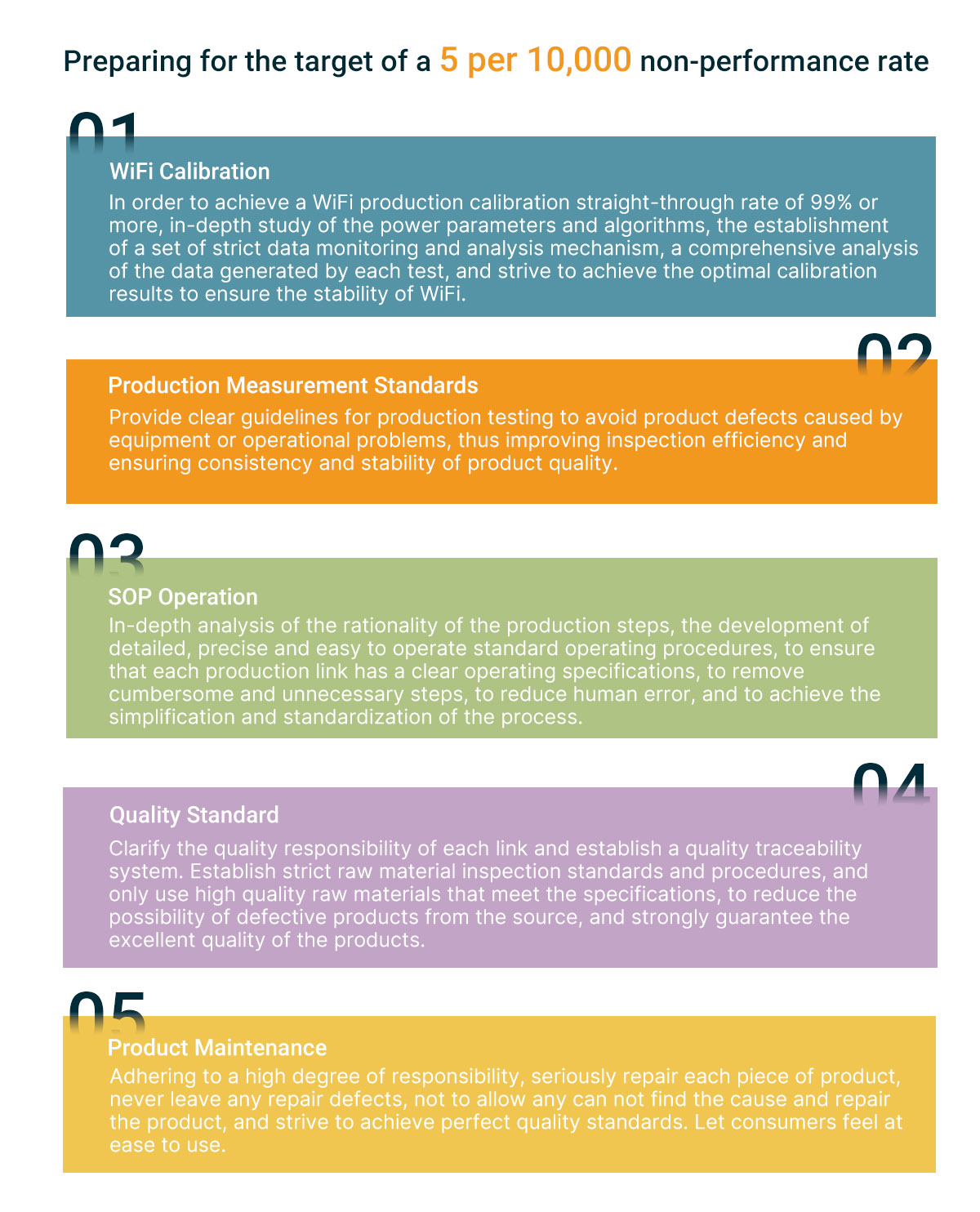
In order to achieve the WiFi production calibration straight-through rate of 99% or more, it is crucial to actively establish and formulate a detailed quality inspection system and standardized processes to ensure smooth production in many key aspects. For example, the "Production Testing Standards" provide clear production testing guidelines to avoid product defects caused by equipment or operational problems, thereby improving testing efficiency and ensuring the consistency and stability of product quality. Product maintenance: We always adhere to a high sense of responsibility and carefully repair every product. We will never leave any repair defects, and we will not allow any unexplained or poorly repaired products, striving to achieve perfect quality standards. Quickly and accurately judge the fault type and severity, and determine maintenance priorities and strategies;Repaired products undergo strict testing, aging and quality inspection processes to ensure the stability and reliability of product performance, allowing consumers to use them with confidence.
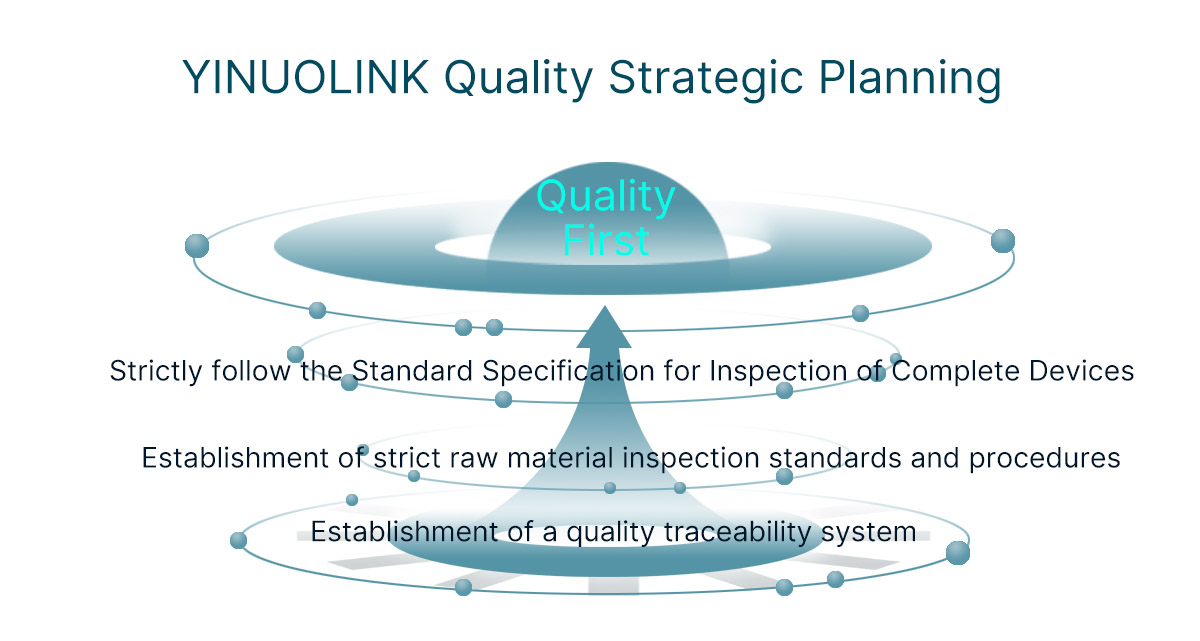
Comprehensively improve the SOP information of all products, work closely with the production department to carry out SOP exercises, analyze the reasonableness of the production steps in depth, and formulate detailed, precise and easy-to-operate standard operating procedures to ensure that each production link has a clear operating specification, remove cumbersome and unnecessary steps, reduce human errors, and realize the simplification and standardization of the process. Regular training and provision of on-site guidance and demonstrations to ensure that employees have an in-depth understanding of and are proficient in the content and requirements of SOPs. During the production process, we closely monitor the alignment between operations and the SOP, discover problems in a timely manner and improve the SOP, so that the SOP is always highly consistent with the actual production situation, so as to effectively guide production operations and continuously improve production efficiency and product quality, and reduce the incidence of errors.
In terms of product quality standards, clarify the quality responsibility of each link and establish a quality traceability system. Strict raw material inspection standards and procedures are established, and only high-quality, specification- compliant raw materials are used to minimize the possibility of defective products from the source and strongly guarantee the excellent quality of products. Before production, the R&D team strictly follows the "First Article Confirmation (SMT/DIP) Process and Management System" to be able to detect potential quality hazards such as design defects, process problems and raw material defects, and take corrective measures in time to reduce the uncertainty in production, so that the production plan can be carried out smoothly and the production cycle of the product can be shortened. In the production, strengthen the supervision and inspection of the implementation of quality standards, strictly follow the corresponding "Finished Product Whole Machine Inspection Standard Specification", once found unqualified products, timely isolation, marking, and never allow it to flow into the next process or the market, and organize the relevant personnel to carry out in-depth analysis, find out the reasons, and formulate corrective measures, in order to prevent the recurrence of similar problems.
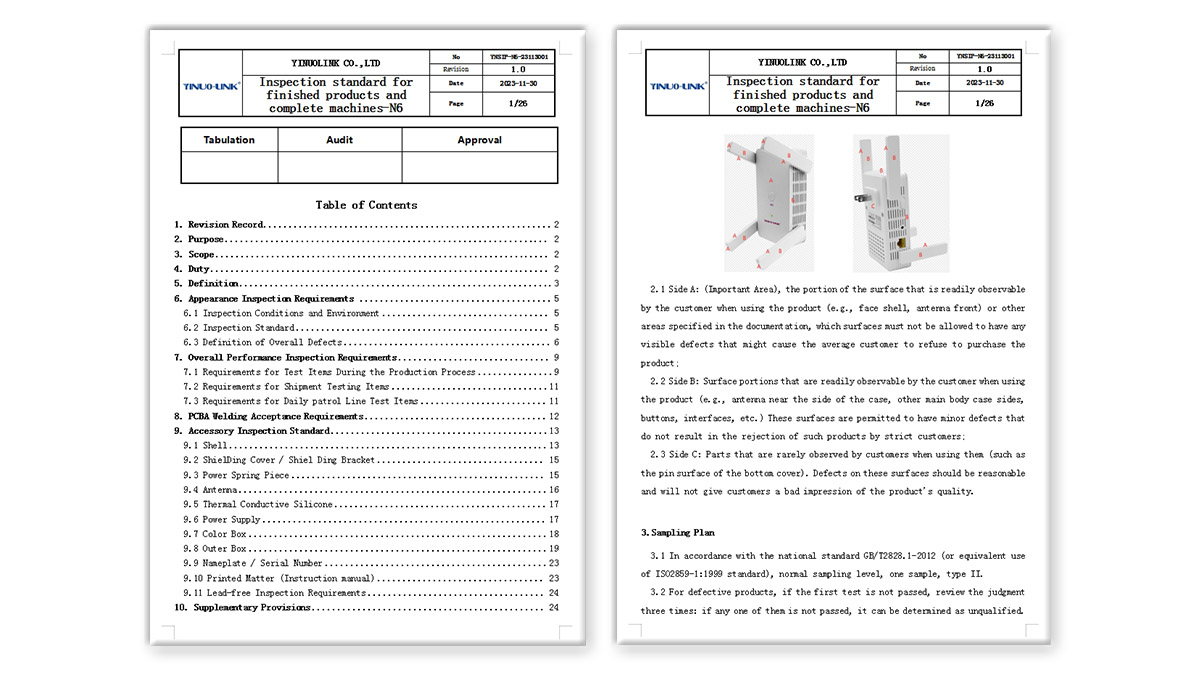
Optimize the supply chain to provide more security for products
Construct a comprehensive and detailed supplier ledger, and implement classification management for multiple brands such as original supplier, agent, and distributor. Continuously improve the supplier management system, formulate a series of standardized documents such as various "PCB Quality Agreement", "Processing Contract", "Environmental Protection Commitment", "Confidentiality Agreement", "Supplier Integrity Agreement", "Entrusted Agent Import Contracts and Agreements", "Overseas Freight Forwarding Agent Export Contracts and Agreements", "Moulds Contracts and Agreements" and so on, and timely replenish the suppliers with the missing information to ensure that the supplier information is Complete and accurate supplier information. Proactively maintain open and good communication with suppliers, strengthen the quality concepts of all parties, and promptly and efficiently identify and solve a variety of potential problems. At the same time, increase the supervision of product quality. When providing samples, strictly require suppliers to issue relevant quality control documents such as "Material Specifications" and "Test Reports". Determine the samples in a timely manner, collect the "Material Acknowledgment Letter" after confirmation, and manage the sealed sample materials. Further optimize the supply chain management system, attach importance to the cooperative relationship with supplier partners, strive to establish long-term and stable cooperative partnerships, and work together with all parties to comprehensively improve production efficiency and quality, reduce costs, and enhance the flexibility and reliability of the supply chain, jointly explore opportunities for innovation and improvement in order to provide better products and services, ensure the long-term stable and smooth operation of the supply chain, and provide a solid guarantee for the sustainable development of the enterprise.
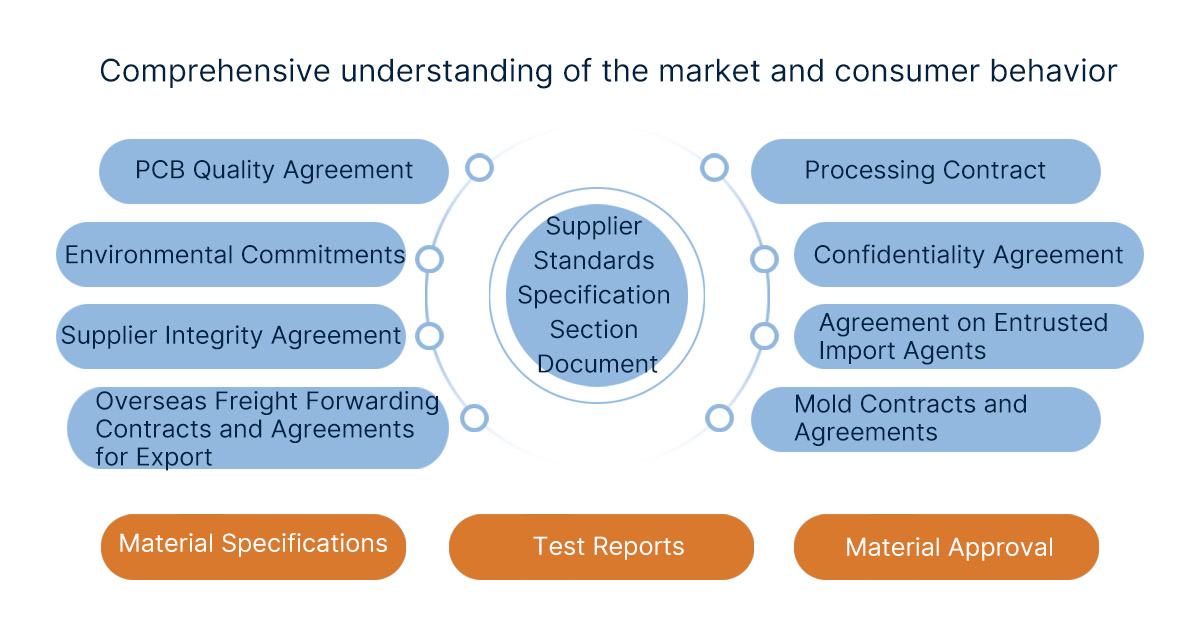
Take the initiative and develop a new chapter in market layout
Market-oriented, actively adjust market strategies. In order to strengthen synergies and cooperation between platforms and realize resource sharing and complementary advantages, the old official website is undergoing a drastic and innovative reform. The new official website has a distinctive style and clear sections. Users can easily obtain service information such as driver installation packages, manuals, and videos that are closely related to the product. A complete website data analysis system monitors website visits, user behavior, traffic sources and other data in real time, and continuously optimizes the layout, content and functions of the website based on data analysis results to better meet market demand and user expectations and improve user experience. Through the Corporate WeChat Official Account, high-quality soft articles are regularly pushed to provide users with the latest industry news and product information.
In terms of platform expansion, on the basis of maintaining the original platforms (such as Alibaba, 1688, and Global Source), Taobao, China TikTok, Google and other platforms have been expanded, thereby further broadening market coverage and increasing the company's exposure and product sales channels, attracting many new potential customers. In addition, multiple platforms provide richer data sources, which help to understand the market and consumer behavior more comprehensively and provide strong support for decision-making.
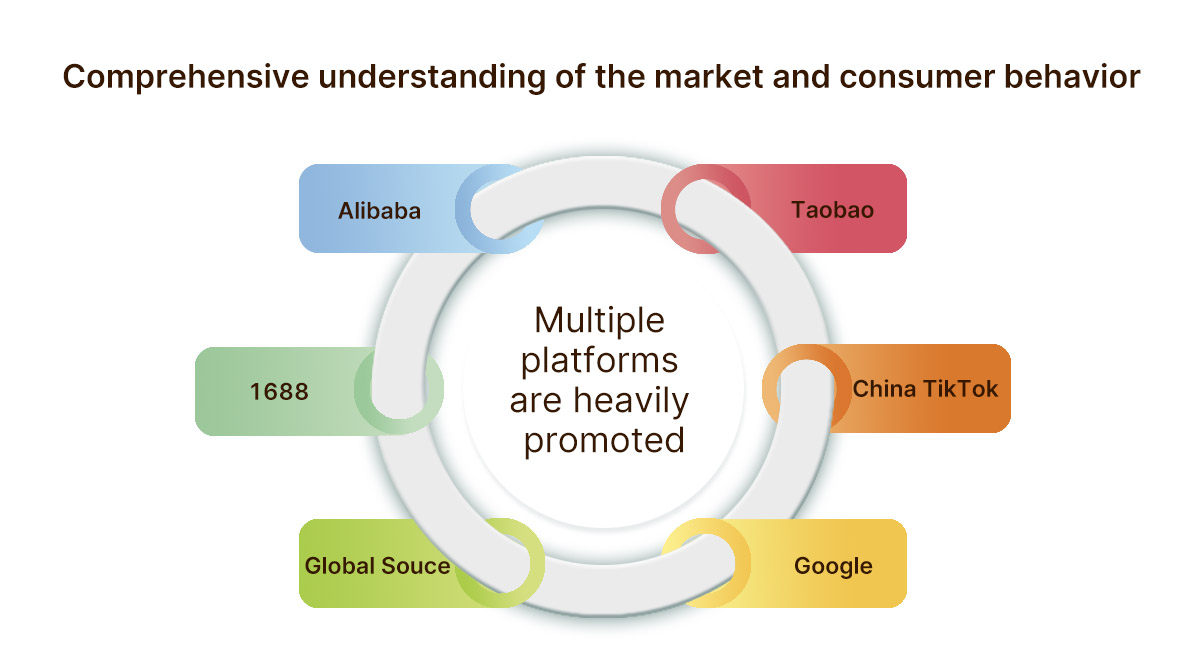
In addition, we actively participate in major international exhibitions, such as the BBWF-Network X 2023 and the 30th Mobile World Congress (MWC24). This action not only enhances close communication with the international market but also attracts a lot of attention. It also successfully reaches cooperation intentions with some well-known international companies, expanding its overseas market share to a certain extent. Through exchanges and observations at the exhibition, enterprises can obtain the latest international industry dynamics and market trends, providing valuable references for their R&D and strategic decisions.
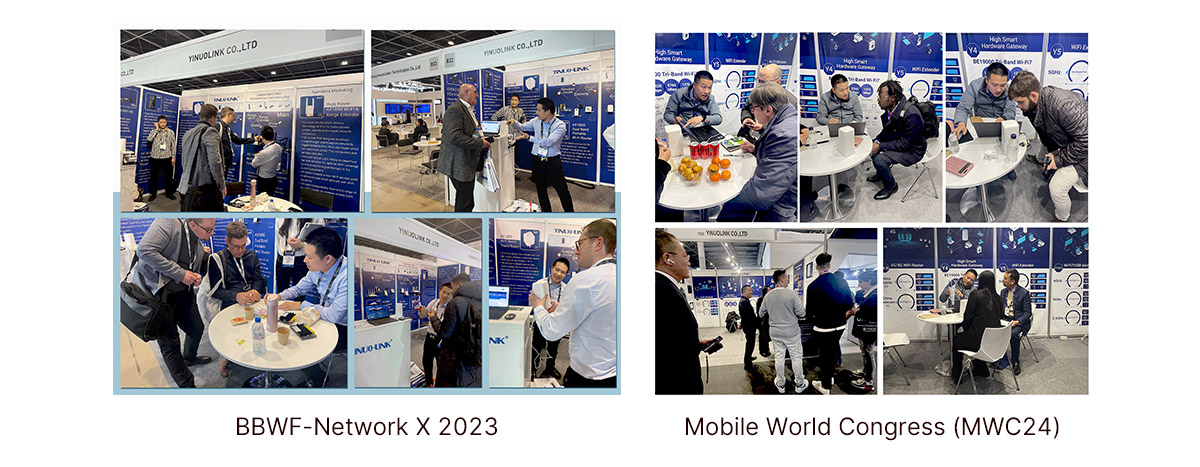
While YINUOLINK pushes forward the product planning and development in an orderly manner, the original customization business also continues to make great efforts to provide exclusive and high-quality solutions for high-end customers and customers with special needs, effectively broadening the market area.
Three Years of Endeavor and Glory
After three years, both hardware and software design have become more and more mature and steady, and now we have successfully launched a series of competitive Mini routers, wireless routers, wireless extenders, mobile WiFi, gateways, network cards, switches, etc., which cover a wide range of fields, such as wireless LAN, broadband access, Ethernet, wireless mapping and transmission, smart home, cloud computing, edge computing, data storage and so on.These products have won widespread recognition and praise in terms of performance, quality and functionality. Since 2024, order volume and sales have continued to rise and breakthroughs have been made.In addition, YINUOLINK has also won dozens of certificates for utility models, design patents, multiple computer software copyrights, and the title of national-level technology-based small and medium-sized enterprises.Its planned products strictly follow global SRRC, FCC, CE, ROSH and other relevant standards.Not only that, we are actively cooperating with top domestic laboratories. By leveraging their advanced technology and professional knowledge, we conduct comprehensive testing and optimization of products. So far, some products have successfully obtained the corresponding certifications.The three-year product plan was successfully completed.
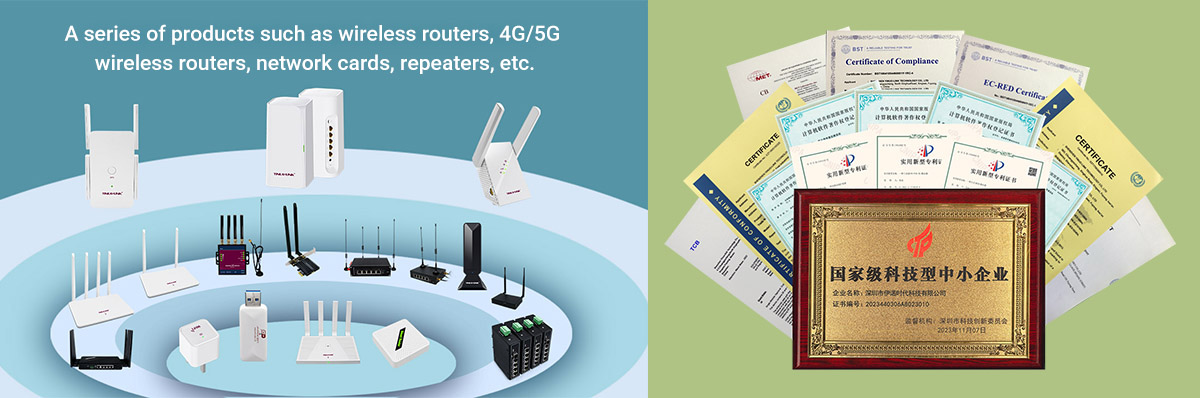
Gratitude for companionship, fulfillment of the future
Looking back, the trust and recognition of our customers are like the light that illuminates our way forward, inspiring us to move forward in the pursuit of excellence. The strong support and cooperation of our supplier partners gives us a solid backing. The unity and cooperation among the YINUOLINK team and the unflinching and all-out spirit when facing various challenges help the company continue to fight bravely. It is because of the trust of customers, the support of suppliers and partners, as well as the strong cohesion and centripetal force among the team that YINUOLINK can move forward in difficult times, break through the barrier again and again, and achieve today's results. Of course, YINUOLINK always upholds a sincere and responsible attitude, delivering high-quality products, paying on time and offering generous benefits as a sincere reward.
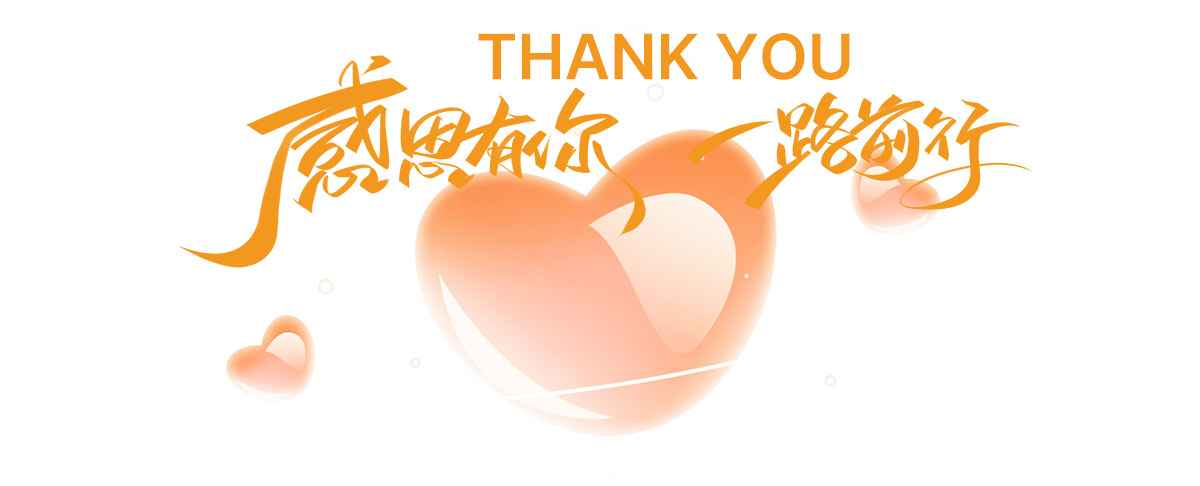
Facing difficulties and striving for excellence
Although YINUOLINK has successfully achieved the set goals of product planning, it still has many shortcomings.
At the product technology level, it is also necessary to gradually optimize product software to test minor bugs, actively explore cutting-edge technologies, and constantly pursue breakthroughs to improve product performance and functionality.
In terms of manufacturing, R&D and production are always in close contact with each other, and we continue to provide professional technical guidance to the production department, optimize the production and testing process and improve the detailed quality inspection system, so as to provide clear quality control guidelines for the production department, and thus enhance the production efficiency. In addition, the production department strengthens the management and supervision of the production site, and strictly controls the quality standard of each production link.
We attach great importance to the optimization of internal management of the enterprise and continuously promote refined management covering human resources, finance, business processes and other aspects to reduce blindness and randomness in decision-making, effectively promote the overall development of the enterprise, and enhance market competitiveness and adaptability.
If the ideal goal has not been achieved in the market field, it is necessary to continue to maintain a high degree of vigilance, always pay close attention to the ever-changing market, take a more proactive attitude to explore the market field, and flexibly adjust market strategies to ensure a firm foothold in the fierce market competition.
We continue to maintain an effective coordination and communication mechanism with our suppliers to strengthen the quality concepts of all parties to ensure that both parties are able to complete deliveries on time and ensure the smooth running of production and operations. At the same time, corresponding early warning mechanisms and response strategies have been established to ensure that the entire supply chain system is always in good operating condition and provide a solid guarantee for the sustainable development of the enterprise. Of course, with the company's steady growth, it is also necessary to continuously strengthen the supply chain management system, continue to deeply develop and optimize the integration of supply chain resources, and add new vitality and competitiveness to the existing supply chain system.
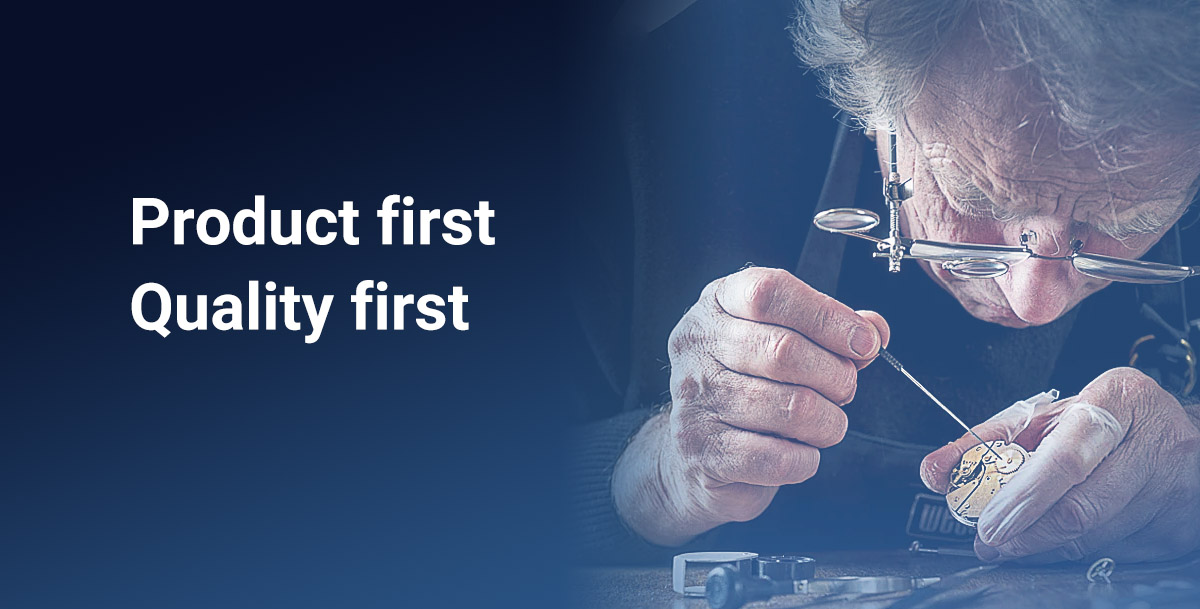
Looking to the future, endless possibilities
Since its establishment, YINUOLINK has always adhered to the spirit of innovation and entrepreneurship, and regarded quality as the lifeblood of the enterprise. Only excellent quality can win the market and the long-term trust of customers.
In terms of product creation, we will continue to increase our efforts, deeply optimize existing deficiencies in software and hardware, and strive to achieve technological breakthroughs to achieve all-round optimization and upgrades. In terms of technology research and development, we are market-oriented and will further go all out to conduct in-depth research on Wi-Fi 7 cutting-edge software/hardware technology, and lay out strategically important products such as high-end industrial routers/Ethernet switches.
In order to fundamentally improve product quality, we have comprehensively established the concept standards of the "Overall Company Quality Strategic Plan", integrated quality awareness into every detail and process of work, and allowed all employees to deeply understand and practice the principle of quality first. Whether from design to testing, or from raw material selection to production technology, we take high-standard quality requirements as the criterion to ensure that products meet high-quality standards at every stage, so as to firmly occupy a place in the market.
In the field of marketing, we develop more targeted and differentiated marketing strategies, deeply explore the needs and pain points of target customers, and enhance the company's visibility and market share through precise market positioning and effective promotion methods.
Strengthen the training and introduction of talents, conduct regular internal communication and sharing meetings, improve performance appraisal and incentive mechanisms, create a positive corporate culture, enhance employees' sense of belonging, enhance team cohesion, and promote the common progress of the team;At the same time, we continue to improve the welfare system, such as providing competitive salaries, generous year-end bonuses, regular team-building activities, etc., to attract all kinds of outstanding talents to actively join, and to inject new energy into the development of the enterprise by continuously enriching the talent team. Vitality and motivation also provide a strong guarantee for the continued growth of the team.
We firmly believe that only by adhering to customer first can we win the trust and loyalty of our customers. Only by adhering to win-win cooperation can we remain invincible in the fierce market competition and achieve sustainable development and growth of the enterprise.
YINUOLINK has always adhered to the original intention, keeping the concept of "Product first, Quality first", and always be committed to improving the product, and making the best quality.